【电镀金刚石切割线图片】_电镀金刚石服务商_电镀金刚石切割线(联系我们)
2021-01-20 09:06:39
关于电镀工具操作的卫生规范:①操作人员进入电镀车间穿工作服,换工作鞋,禁止非工作人员随便进入车间。②每天工作完毕,仔细清理操作场地;定期清理车间设备和电镀容器、辅助用具等,除去灰尘和盐类结晶物,保持设
关于电镀工具操作的卫生规范:
①操作人员进入电镀车间穿工作服电镀金刚石切割线,换工作鞋电镀金刚石,禁止非工作人员随便进入车间。
②每天工作完毕,仔细清理操作场地;定期清理车间设备和电镀容器、辅助用具等,除去灰尘和盐类结晶物,保持设备整洁和运行正常。
③电镀设备停用时加罩加盖(尤其电镀槽和盛砂容器),保持清洁。
④车问禁止堆放非生产用的杂物,减少尘埃源。
气孔在磨削时对磨屑起容屑和排屑作用,并可容纳冷却液电镀金刚石刀具,有助于磨削热量的散逸。为满足某些特殊加工要求,气孔内还可以浸渍某些填充剂,如和石蜡等,以改善磨具的使用性能。这种填充剂,也被称为磨具的第四要素。
电阻率及耐腐蚀性
表面电阻率是称量膜层耐蚀性的重要指标。类金刚石膜表面电阻高,在腐蚀介质中表面出极高的化学惰性,从而保护基底金属免遭外界腐蚀介质的溶蚀电镀金刚石工具。一般含氢的DLC膜电阴率比不含氢的DLC膜的高,这也许是氢稳定了sp3键的缘故。沉积工艺对DLC膜遥电阴率有影响,另外离子束能量对类金刚石膜层电阴率也有较大的影响,随着离子束能量增加大阴率增大。
沉积金刚石薄膜的机理至今尚无定论
磨料磨具中低温低压下CVD法沉积金刚石薄膜的机理至今尚无定论,仍是今后的研究方向之一。晶体的形成分为两个阶段,早阶段称为晶体成核阶段,第二阶段晶体生长阶段。早阶段含碳的气源在合适的工艺参数下,在沉积基体上形成一定数量的孤立的金刚石晶核;第二阶段,金刚石晶核不断长大,并连成一片,覆盖整个基体的表面,再沿垂直方向生长,形成一定厚度的金刚石膜。
在早阶段主要目的是尽快的在基体表面上形成金刚石晶核,并能有效的控制金刚石的密度,要大限度的提高金刚石的形核密度;在第二阶段主要目的是让已形核的金刚石长大,并能有效的控制金刚石膜的生长速度和质量。
砂轮削磨的普通冷却方法
1.砂轮磨削液选择不当,选择合理的砂轮磨削液。一般选择油性的砂轮磨削液,降低了砂轮磨削区的温度,会适当减少伤害的发生。在有条件的情况下选择品牌的砂轮磨削液。
2.可在采取湿磨的情况下一定不采用干磨。
3.砂轮磨削液有效充分供给,不但要砂轮磨削区供给充足,而且压力要大;才可以让温度降低与充分排屑。
4.保持冷却液的纯净。
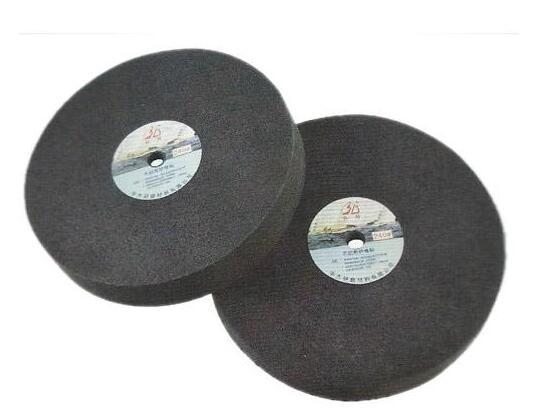
5.保持冷却液较低的温度,从而可以降低砂轮磨削区的温度,必要时可使用散热器。
6.砂轮磨削液喷嘴安放位置不妥,应使喷嘴尽可能靠近砂轮磨削区。
7.冷却液喷嘴加装空气挡板。
8.使用内冷却砂轮:内冷却法是将经过严格过滤的冷却液通过中空主轴引入砂轮的中空腔内。由于离心力的作用,将切削液沿砂轮孔隙向四周甩出,直接冷却砂轮磨削区。
埋砂法复合电沉积金刚石磨轮工艺流程
埋砂法复合电沉积金刚石磨轮工艺流程为:金属清洗剂脱脂—清洗―防镑处理—做阻镀 ―上挂具―浸盐酸—清洗―电解酸蚀—清洗—带电入槽预镀—入砂罩植砂―固砂—补植砂—固砂 ―转动下加厚镀—出槽清洗—下挂具―清除阻镀 ―上挂具―浸盐酸―清洗—化学镀镍或其它表面 保护处理―清洗—干燥—下挂具―检验—包装。
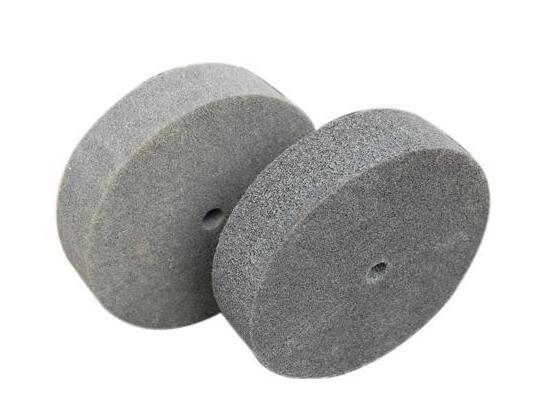
植砂:将金刚石牢固镶嵌在金属基体上是保证电镀 金刚石制品的关键。轨道板磨轮基体质量达124 kg,且型面不一,据了解国内制造厂家大都使用经典 的撒砂法即把经预镀的工件置于镀液内,并将每个需要植砂的型面几经转或移动分别在处于水平位置的型面撒上d为425-600 μm的金刚石颗粒,每撒一型面施镀1 h左右,一般需经12次左右的镶嵌 镀覆才可使基体各型面完成植砂。
新型数字智能磨边机
新型数字智能磨边机将过去磨边机靠人工观察和操作的工作,如今都可以通过数字化、自动化完成,从而能够减轻操作人员劳动强度。对操作人员的专业技能要求大大降低,对提升瓷砖优等品率,保证生产稳定也大有益处。
这一改变得益于推砖机构的改进。以往的推砖机构当砖的对角线超差时就需要停机调节,或者不停机在推砖动作时人到推砖架上进行调节,这样的弊端是显而易见的。

需要多次调整,效率低,过程中会有部分砖超差降级,且对磨边工的经验要求较高。如果停机调节影响生产,不停机调整又有安全隐患。
数字智能磨边机配备了新型的推砖机构,其中一个推砖爪可以进行伺服电动调节,通过对磨边后成品砖的对角线长度尺寸进行检测。当测量两条对角线长度尺寸差超过限定值后,其中一个推砖爪可通过在操作屏上直接输入前后位置的调整量,执行机构可在两次推砖动作的间隙电动完成调整,从而完成入砖角度的调整。