专业提供电镀金刚石刀具报价_电镀金刚石刀具批发
2021-05-10 09:05:42
金刚石薄膜的优点金刚石薄膜的优点是可应用于各种几何形状复杂的刀具,如带有切屑的刀片、端铣刀、铰刀及钻头;可以用来切削许多非金属材料,切削时切削力小、变形小、工作平稳、磨损慢、工件不易变形,适用于工件材
金刚石薄膜的优点
金刚石薄膜的优点是可应用于各种几何形状复杂的刀具,如带有切屑的刀片、端铣刀、铰刀及钻头;可以用来切削许多非金属材料,切削时切削力小、变形小、工作平稳、磨损慢、工件不易变形,适用于工件材质好、公差小的精加工电镀金刚石刀具。主要缺点是金刚石薄膜与基体的粘接力较差电镀金刚石,金刚石薄膜刀具不具有重磨性。
带柄磨头/小砂轮:磨头的种类很多,有陶瓷磨头,有橡胶磨头,供应商可以根据磨料和结合剂的不同进行选择;磨头有很多形状,而且每个公司对磨头形状代号没有统一,本文只列举了目前比较常见的形状供选择。“数量”属性是专门为磨头套装分类设置的,收集了目前比较常见的套装数量供选择。
金刚石刀具的限制:
重磨和重涂层的金刚石涂层刀具质量难以保证由于刀具表面生成的涂层为纯金刚石,因此用金刚石磨轮对刀具进行重磨需要耗费很长时间电镀金刚石刀具。
此外,为使金刚石生长而采用的刀具。制备工艺会改变刀具表面的化学特性,由于涂层时要求对这种化学特性进行非常准确的控制,因此刀具重新涂层的效果难以得到保证。
金刚石通过不同的金属镀覆,再经X射线衍射研究分析表明:金刚石表面形成各种不同的碳化物,而产生新的化学键合,提高了金刚石把持力,金刚石颗粒与胎体金属形成“化学/冶金结合”,增加金刚石与胎体之间结合强度,并能抵抗对金刚石的氧化与石墨化,提高金刚石工具的使用寿命,完善了金刚石工具使用性能。
含金刚石的金属镀层中镀层金属层状分离
含金刚石的金属镀层在使用过程中,与工件接触部分的镀层金属不是正常磨耗,而是非正常地成片或粉末状脱落,金刚石不是全部脱落,而是局部粒状脱落。
优化镀液配方和电镀工艺、采取带电入槽,防止双极性现象,对于形状复杂的工件采用短时间大电流冲击空镀,以减少镀层内应力和析氢现象的影响,提高镀层质量。
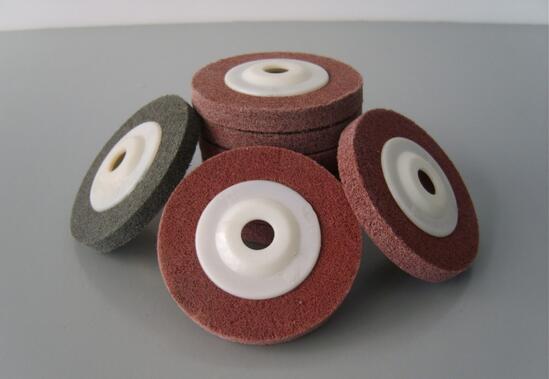
优化工艺、工序,减少卸砂时的断电时间,甚至不断电在原上砂槽内卸砂、加厚或在一备用槽内带电卸砂,以提高金刚石颗粒与镀层间的结合力。若在加厚过程中遇停电现象,重新加厚时,工件应放入电解液中进行阴极还原,还原后带电入槽电镀以保证镀层结合力。
金刚石工具
金刚石工具是在预先加工成型且形状各异的金属基体表面,用复合电镀的方法镶嵌一层(表镶)或多层(孕镶)金刚石颗粒而制成,如金刚石磨具和钻具。在生产现场将复合镀层中的基质金属称作胎体,的为Ni、Ni-Co、Ni-Fe和Ni-Mn合金以及近年来引起重视的Ni-Co-Mn合金。
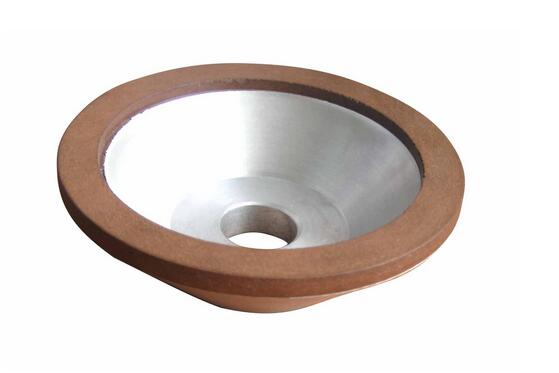
胎体各具特性,在制造复合电镀金刚石工具时对复合镀层的硬度、平整性、金刚石与基质金属间的结合力及使用寿命有很高的要求,一般多采用w(Co)为30%以下的Ni-Co合金做基质金属。
镀液中依金刚石的平均粒径
一般加工玉雕的磨具钻具形状繁杂,尺寸各异,大都采用埋砂法,给工具基体上粘上一层金刚石,即将固定于夹具上的待镀件预镀后,置于盛有金刚石,溶液可以自由流通的非金属砂槽内,在镀液中依金刚石的平均粒径。
电镀时间,使金刚石被镶于工件表面,一般掌握嵌入率达到10%左右即可,嵌入率太低,对金刚石的粘附欠牢,加厚镀时易被吹落,过厚则易“糊”活,且往往会使磨粒搭桥架空,在加厚镀时覆盖在工具上的金属镀层,在磨削时将在该处造成爆裂。
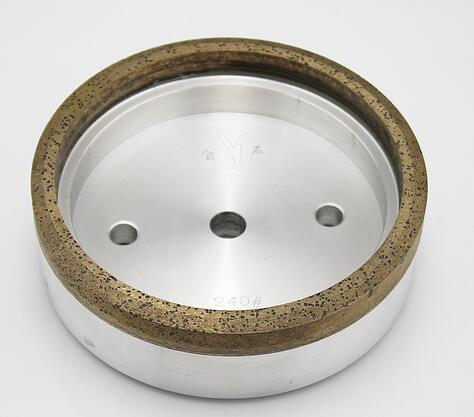
镶砂的Jκ应依据金刚石平均粒径控制,如金刚石颗粒d为49μm的上砂用0.5A/dm2电镀25~30min,金刚石颗粒d为196μm的上砂用0.75A/dm2电镀60min为常用,以使金刚石尽可能单层均布于待镶工作部位。
磨边机如何判断磨头切削量
每台磨边机几十个磨头,每个磨头的切削量是多少,过去一直都是靠人工听声音,看火花这样原始的方式观察判断,磨边操作就成了经验活。而在该设备上,每个磨头有磨轮损耗数字变量显示,每个磨头配置有数字电流表,只要察看操作屏上的磨轮损耗变量值和电流数值,就能判断磨头工作状况,很容易确认磨轮是否需要进给和进给多少。当磨轮损耗完后,设备自动报警提示,方便及时更换。
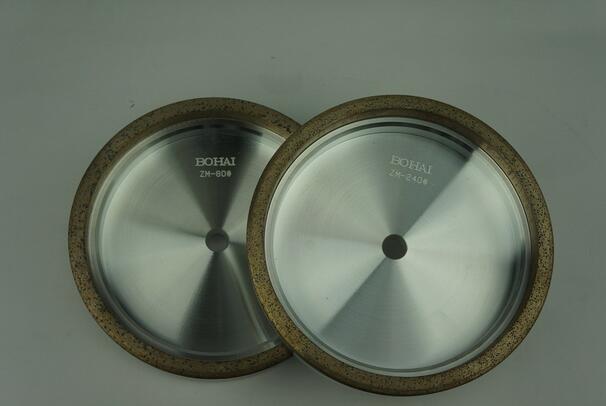
每台机的后两组磨边头的电动调节也可以与尺寸检测仪关联,形成闭环控制。一旦砖的对边尺寸检测超差,磨边头会根据反馈数字信号自动调节磨边轮的前后位置,修正磨边尺寸,控制砖的尺寸在设定范围内。